As a civil engineering pupil, I had the chance to discover varied branches of engineering, together with electrical. Throughout this journey, I used to be launched to printed circuit board (PCB) design, and I used to be fascinated by the method of making circuits and understanding how every element works collectively to type a purposeful design.
I shortly discovered that selecting the finest PCB design software program is essential to making sure environment friendly, dependable, and high-quality designs. The correct software program streamlines the design course of, supplies strong instruments for routing, simulating, and validating circuits, and helps handle complexity whereas guaranteeing the ultimate product meets all technical necessities.
Quick-forward to as we speak—I’ve examined a variety of PCB design software program instruments to guage their efficiency, usability, and options. With so many choices out there, it was essential for me to dive deep and assess how every instrument handles real-world initiatives.
By mixing my private testing expertise with helpful suggestions from G2 customers, I’ve compiled a listing of the 7 finest PCB design software program that will help you discover one of the best match to your personal initiatives.
7 finest PCB design software program: My picks for 2025
- Altium Designer for its superior design instruments and in depth element library ($355/mo)
- Altium 365 for its PCB format editor and 3D visualization capabilities (Price relies on connectors chosen)
- PADS Skilled for its capacity to deal with complicated PCB layouts and superior routing options ($286.92/mo)
- Allegro PCB Designer for its capacity to handle high-density PCB designs and error correction programs (Out there on request)
- Autodesk Fusion for its built-in method to mechanical and electrical design, together with 3D design capabilities ($85/mo)
- Altium CircuitMaker for being a community-driven, open-source PCB design instrument (Free)
- Autodesk EAGLE for its intuitive consumer interface and schematic seize capabilities (Out there on request)
* These PCB design software program are top-rated of their class, in accordance with G2 Grid Experiences.
My high 7 finest PCB design software program suggestions for 2025
PCB design software program is a robust instrument used to create and optimize printed circuit board layouts. It helps engineers design the digital circuits that type the spine of recent units.
As I explored one of the best PCB design software program, I discovered they provide greater than primary format capabilities. They supply superior options equivalent to real-time collaboration, 3D visualization, and error-checking.
Testing varied instruments on small initiatives allowed me to establish options that improved the design course of whereas additionally serving to me relive my engineering days. On this article, I’ll spotlight what made these instruments stand out and the way they helped me overcome widespread design challenges.
How did I discover and consider one of the best PCB design software program?
I extensively examined one of the best PCB design software program to create, optimize, and handle PCB layouts. To deepen my understanding, I additionally linked with electrical engineers to find out about their wants and challenges when designing PCBs and utilizing these instruments. Moreover, I used AI to investigate G2 consumer suggestions and G2’s Grid Experiences to achieve additional insights into every instrument’s options, ease of use, and general worth. By combining hands-on testing with professional insights and consumer critiques, I’ve curated a listing of one of the best PCB design software program that will help you select the fitting instrument to your design wants.
What I search for in PCB design software program
When evaluating PCB design instruments, I take into account options that streamline the design course of, improve effectivity, and make sure the creation of high-quality, dependable circuits:
- Superior routing capabilities are important for complicated designs. The software program ought to permit for fast automated routing of traces, particularly in multi-layer PCBs, however it should additionally let me make handbook changes to fine-tune the sign paths. It ought to deal with layer transitions easily, routing alerts by internal layers utilizing vias. By way of stitching is essential for creating an excellent floor or energy aircraft, which helps cut back noise and enhance sign high quality. The software program also needs to help impedance-controlled routing to make sure the traces meet particular impedance necessities, which is essential for high-speed circuits. Lastly, it ought to let me modify hint width and clearance to satisfy manufacturing and electrical requirements.
- Design rule checks (DRC) are important for me to establish potential design errors earlier than transferring into manufacturing. The software program I exploit should present customizable DRC settings that assist examine for violations of design constraints like hint width, pad sizes, through dimensions, and clearance between traces, pads, and vias. I would like to have the ability to create guidelines based mostly on the fabrication capabilities of the PCB producer, equivalent to minimal hint width and most present carrying capability. The software program ought to robotically flag errors like hint overlap, unconnected nets, or element misplacement and generate an easy-to-read report for additional evaluation so I can tackle points early.
- Electrical rule checks (ERC) are simply as essential to make sure the circuit capabilities appropriately. ERC helps me catch points associated to {the electrical} connectivity of parts and alerts, equivalent to unconnected nets, energy/floor shorts, and incorrect element values. The software program should be certain that all parts are linked as proven within the schematic and that no unintended electrical paths are created. For instance, it ought to examine for floating pins on built-in circuits (IC), mismatched energy rails, and incorrect internet assignments. In high-speed designs, ERC also needs to be able to figuring out potential sign integrity points, equivalent to unbalanced differential pairs and floor bounce, which might have an effect on circuit efficiency.
- Help for multi-layer PCB designs, particularly for high-density or high-performance purposes, multi-layer PCBs are sometimes required. The software program I exploit ought to permit for the seamless creation of four-layer, six-layer, or much more complicated designs. It’s essential for me to have the ability to outline layer stacks, with internal layers used for routing and outer layers for element placement. The instrument should additionally help energy and floor planes to make sure electrical stability by minimizing electromagnetic interference (EMI). Moreover, the power to deal with blind vias (vias that don’t undergo all layers) and buried vias (vias that solely join internal layers) is essential for maintaining the design compact. The software program also needs to robotically optimize the routing between layers and effectively handle each sign integrity and energy integrity in multi-layer configurations, which is essential for high-quality, dependable designs.
- Sign integrity evaluation is crucial for me to make sure that high-speed alerts are transmitted with out degradation. The software program I exploit should come geared up with SI simulation instruments that analyze elements like hint impedance, sign reflection, crosstalk, and electromagnetic interference (EMI). These instruments assist me perceive how alerts behave on the PCB and guarantee they continue to be dependable, particularly in complicated designs. Options like sign path evaluation and eye diagrams are essential as a result of they permit me to visualise the standard of sign transmission and examine for any points that might have an effect on efficiency. This provides me confidence that the design will meet the required sign integrity requirements.
- As somebody new to instrument testing, having a complete element library is a big time-saver for me. The software program ought to include a variety of widespread parts, every together with correct footprints, symbols, and 3D fashions, which makes it a lot simpler to get began without having to manually create every half. When working with customized parts, the software program should permit me to simply create and modify footprints and symbols, which helps me outline essential parameters like pad dimension, gap diameter, and pitch. This ensures that every one parts match appropriately on the PCB.
- 3D visualization is invaluable for verifying the bodily format of the PCB. This function lets me view the PCB in three dimensions to establish potential mechanical conflicts, equivalent to parts which will collide with the enclosure or different elements of the design. It helps confirm element orientation and clearances between parts and traces. Moreover, the power to simulate meeting in 3D can be certain that all parts match as supposed earlier than manufacturing, stopping expensive redesigns. The 3D mannequin additionally aids in confirming the mechanical integrity of the board, guaranteeing there’s sufficient stiffness and help for parts which will expertise bodily stress throughout operation.
- Collaboration instruments are important when working in a group surroundings. I search for software program that helps cloud-based design sharing, permitting for seamless real-time collaboration amongst group members, no matter location. The power to implement model management inside the design instrument is important for monitoring modifications and stopping unintentional overwrites of crucial information. I choose instruments that permit feedback and annotations inside the design information in order that the complete group can talk about and resolve points straight inside the software program. This function is especially helpful for groups that work in iterative design cycles or when integrating suggestions from varied stakeholders. Design historical past monitoring ensures that I can revert to earlier variations of the design if crucial.
The record under incorporates real consumer critiques from our greatest PCB design software program class web page. To qualify for inclusion within the class, a product should:
- Modify PCB layouts and PCB circuitry
- Embody a parts library so customers can simply implement high-quality PCB footprints
- Present schematic modifying instruments for modification {of electrical} properties and different attributes of parts, wires, nets, and pins.
This information has been pulled from G2 in 2025. Some critiques have been edited for readability.
1. Altium Designer
Altium Designer provides a unified platform that integrates totally different design instruments, together with schematic seize, format routing, documentation, and simulation, into one surroundings. What I recognize most is the power to seamlessly transfer between these phases. For instance, as soon as I create the schematic diagram, I can simply transition to the layout-routing part, adjusting the design whereas visualizing the ultimate product. This clean workflow saves me time and helps me maintain every thing organized without having to modify between a number of instruments or fear about integration points.
A function that basically impressed me is design for manufacturing (DFM). This ensures that designs should not solely purposeful but additionally simple to provide. The DFM instruments assist establish potential points early within the course of, decreasing errors and saving time in the course of the manufacturing part. It’s reassuring to know that my design is optimized for manufacturing earlier than transferring on to precise fabrication.
With the 3D flex-rigid design, I used to be capable of visualize how the totally different layers of a PCB interacted, together with each versatile and inflexible elements. This was particularly helpful when testing extra complicated, multi-layered designs. I can see how seeing how every element interacts in 3D may give producers higher perception and assist them make extra knowledgeable selections whereas routing the format.
Its in depth element library provides an enormous number of elements, parts, and templates, which allowed me to shortly discover what I wanted. This function reduces the necessity to manually design parts from scratch, and I used to be in a position to make use of pre-validated elements that helped decrease errors. The large choice made the method sooner and extra dependable, which is at all times a plus.
The largest concern I confronted was the system necessities. Altium Designer requires lots of reminiscence and processing energy. On high-end machines, the software program runs easily, however on much less highly effective computer systems, I skilled noticeable slowdowns, particularly when coping with bigger, extra complicated initiatives.
Making an attempt to run a number of instruments without delay typically resulted in lag, which made the expertise irritating. For customers with much less highly effective programs, this might actually influence workflow and productiveness.
One other ache level for me was including footprints to units. Whereas Altium provides a big number of footprints, the method felt a bit cumbersome. Discovering the fitting footprint requires navigating by a number of libraries, and there isn’t a easy method to view all out there choices for a element in a single place.
Linking the footprint to the schematic image additionally felt disjointed, because it wasn’t at all times clear if the right one was chosen. There wasn’t a straightforward method to confirm the accuracy of the footprint after it was added, which led to some further steps to make sure every thing was appropriately aligned. I discovered this to be time-consuming and a bit irritating, particularly when making an attempt to work effectively.
The studying curve can be one thing to remember. Altium Designer is filled with options, which is nice for knowledgeable customers however could be overwhelming for newbies like me. The interface is stuffed with choices, and it took me a major period of time to familiarize myself with all of the instruments.
What I like about Altium Designer:
- The unified platform of Altium Designer made it simple for me to maneuver seamlessly between design phases, from schematic seize to format routing. This saved me time and stored every thing organized without having to modify between totally different instruments.
- The DFM function actually impressed me by serving to optimize designs for manufacturing. It allowed me to establish potential points early, cut back errors, and guarantee my design was prepared for fabrication.
What G2 customers like about Altium Designer:
“Altium Designer supplies every thing wanted for design and format in a single instrument, eliminating the necessity for extra purchases. It integrates seamlessly with large-part databases, providing pricing, availability, and environment friendly manufacturing BOM technology. The built-in SPICE instrument helps analog simulation, and its format options embody matched size routing, managed impedance, differential pairs, and each guided handbook and auto-routing, which save important time as soon as mastered. The mixing of 3D mechanical fashions into designs and outputs for mechanical use is extremely helpful. General, Altium Designer is one of the best digital design instrument I’ve ever used.”
– Altium Designer Evaluation, Tim T.
What I dislike about Altium Designer:
- The system necessities for Altium Designer had been difficult for me, because it requires lots of reminiscence and processing energy. On much less highly effective computer systems, I skilled slowdowns and lag, which considerably impacted my workflow, particularly with bigger, extra complicated initiatives.
- Including footprints to units was a irritating course of for me. Navigating by a number of libraries and linking the footprint to the schematic image wasn’t simple, and I discovered myself spending further time verifying every thing was right, which slowed me down.
What G2 customers dislike about Altium Designer:
“One space for enchancment is including extra options to the “Producer Half Search.” Moreover, navigating the software program and not using a mouse could be difficult, particularly when utilizing a laptop computer. Proper-clicking and dragging on a trackpad could be irritating, although that’s partly because of the laptop computer design. One other suggestion pertains to defining board dimension; for example, once I wanted a board that was precisely 50mm x 50mm, it was exhausting to attract exact strains. I ended up setting the grid dimension to 1mm and estimating the scale. It will be useful to have a function that shows the size of line drawings or the scale of the shapes being created.”
– Altium Designer Evaluation, Trevor M.
2. Altium 365
One of many standout options of Altium 365 is its real-time collaboration capabilities. It helped me join with circuit groups on the identical designs concurrently. Whether or not I used to be reviewing schematics or making PCB format changes, it ensured everybody was on the identical web page. The platform’s model management system ensured that each change is tracked, which allowed me to view revision histories or roll again to earlier variations with ease.
It has extremely environment friendly mission administration instruments which have made dealing with complicated designs a lot simpler, particularly once I’m engaged on intricate designs. I discovered the method of making and modifying parts to be each intuitive and highly effective, permitting for detailed work with out feeling overwhelming. I can see how this flexibility could be an enormous asset for groups, enabling them to handle large-scale initiatives with ease.
I’ve additionally actually loved working with the PCB format editor. It’s extremely customizable, which permits me to make changes to designs shortly and seamlessly. I actually appreciated the power to effortlessly transition between schematic and PCB. It saved me lots of time, as I might shortly modify and export designs. For groups that must combine these modifications into their bigger platform-based initiatives, this function would make the complete course of way more environment friendly, significantly when speedy changes are required.
The 3D visualization function was one other space the place Altium 365 impressed me. I used to be capable of visualize how parts match on the board with ease, particularly in tight areas. The software program’s help for .step 3D our bodies made it simple to see how every thing would match collectively. What stood out was the 3D rendering velocity – even when working with complicated parts, they rendered shortly with none noticeable lag. I discovered the “snap factors” function significantly helpful, because it helped me place even essentially the most awkward 3D our bodies with nice precision.
Lastly, the draftsman instrument has been an absolute spotlight. Producing high-quality meeting drawings was a breeze with just some clicks. This instrument allowed me to create detailed and visually interesting drawings, which I might think about could be very useful for manufacturing groups that want clear documentation for meeting.
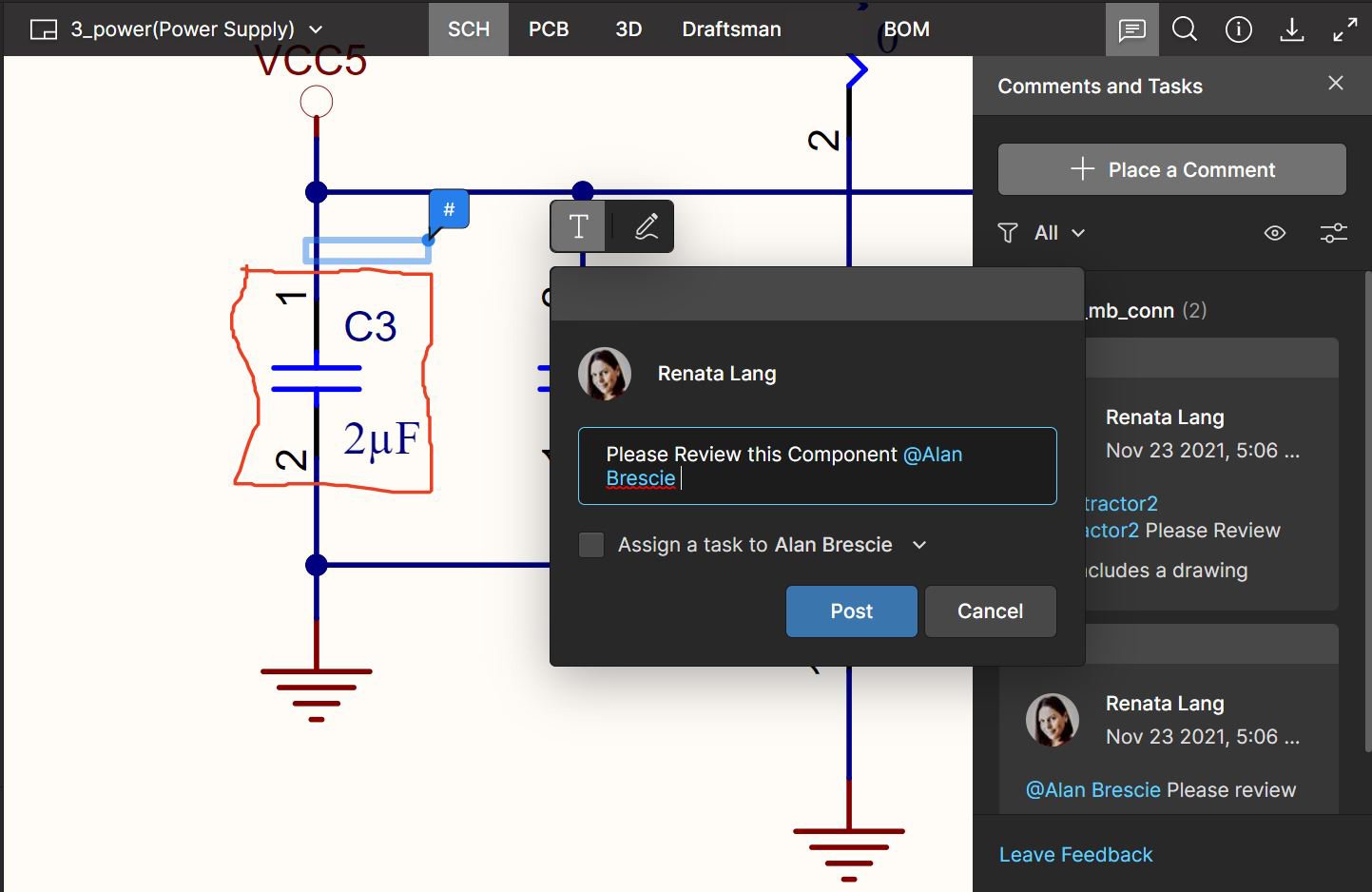
Nonetheless, regardless of these constructive experiences, there are just a few areas the place I feel Altium 365 might enhance. One of many challenges I confronted was with establishing PCB routing guidelines. It required a little bit of programming data, which could not be beginner-friendly. Whereas I ultimately turned proficient, I might see how somebody new to this sort of design software program would possibly discover this function a bit difficult. A extra user-friendly interface for setting these guidelines will surely make the method smoother for newbies.
One other concern I encountered was with the design rule system. Some customized queries didn’t work as anticipated, significantly when making an attempt to arrange guidelines to disregard interfering parts. For instance, I created a “element clearance” rule with particular settings for vertical and horizontal clearance, however the rule didn’t persistently ignore collisions. Regardless of prioritizing the rule appropriately, it did not work on some events, which was irritating.
I additionally bumped into a difficulty with observe size calculation. There have been instances when Altium appeared to disregard small segments of the observe on sure layers, which might be problematic when making an attempt to exactly match observe lengths, particularly for impedance-controlled designs. This led to inaccuracies within the format, requiring me to manually modify and double-check sure areas.
On just a few events, Altium 365 additionally skilled reminiscence violation errors, which had been a bit regarding given the software program’s complexity. Whereas it labored nicely for many of my initiatives, bigger and extra complicated designs prompted the instrument to decelerate, particularly when working over a community. This resulted in longer load instances and delays in accessing information, which might be irritating throughout tight mission timelines.
Lastly, the Invoice of Supplies (BOM) function took longer than anticipated to generate. Moreover, it wanted to be up to date each time I made modifications to the schematic, which added delays to the workflow, particularly when working with frequent design revisions.
What I like about Altium 365:
- Altium 365’s mission and library administration instruments made dealing with complicated designs a lot simpler for me. Their intuitive and highly effective options allowed detailed work with out feeling overwhelming, which might be helpful for groups managing large-scale initiatives.
- The 3D visualization function impressed me, because it allowed me to shortly see how parts match on the board, even in tight areas. Quick rendering and exact placement utilizing the “snap factors” function tremendously enhanced the design course of.
What G2 customers like about Altium 365:
“What I really like most about Altium 365 is how effortlessly it allows cloud-based collaboration, making it supreme for real-time PCB design initiatives, particularly for worldwide groups. Its seamless integration with Altium Designer and the power to entry designs from wherever makes it my go-to instrument, one I exploit virtually each day. For these utilizing model management instruments like Git, the centralized library administration and reusable design choices considerably velocity up growth. The intuitive interface turns into simple to navigate with some preliminary exploration, making it sensible for practically any PCB mission. Plus, the rising neighborhood help is invaluable.”
– Altium 365 Evaluation, Angel O.
What I dislike about Altium 365:
- The setup of PCB routing guidelines required some programming data, which wasn’t very beginner-friendly, making the educational curve steeper for brand spanking new customers. A extra user-friendly interface for these guidelines would enhance the expertise for these simply beginning out.
- I encountered points with the design rule system. Customized queries typically didn’t work as anticipated, particularly with element clearance guidelines, inflicting frustration when the principles did not persistently forestall collisions.
What G2 customers dislike about Altium 365:
“The software program could be sluggish to begin and entry information, particularly over a community. Some default settings, just like the connection matrix, generate pointless warnings that make it tougher to establish actual points. The Invoice of Supplies function takes time to generate and requires updates when modifications are made to the schematic. Moreover, the software program slows down with bigger designs, and whereas it integrates nicely with third-party parts, occasional points with mismatched footprints or image requirements can come up.”
– Altium 365 Evaluation, Hemant A.
3. PADS Skilled
One of many largest strengths I seen about PAD Skilled is its capacity to deal with complicated PCB layouts. This function was significantly helpful once I created intricate designs requiring exact management.
The interactive options, particularly the auto-routing choices, really stood out to me. It sped up the format course of considerably, and I might visually observe the routing because it progressed, which made the complete course of smoother and extra environment friendly.
One other standout side is the in depth documentation. As somebody new to the instrument, I relied closely on the documentation, and it did not disappoint. It lined every thing from primary performance to extra superior choices, serving to me shortly perceive options that might have in any other case been difficult to determine.
I additionally appreciated the schematic half view, which helps you to rotate parts at totally different angles. This was a surprisingly useful function, making it simpler to visualise and work with incessantly used parts, particularly those who want particular orientations.
One of the vital spectacular integrations I got here throughout was the hyperlink to HyperLynx for sign integrity or energy Integrity simulations. I might effortlessly carry out detailed simulations, and the seamless integration actually enhanced the instrument’s capabilities. It felt like having a powerhouse of study at my fingertips.
The versatile design constraint system allowed me to outline particular design guidelines simply. This added precision to designs and ensured compliance with manufacturing necessities. Nonetheless, this function might shine much more if paired with improved usability for template creation.
I discovered the preliminary setup a bit overwhelming. The instrument provides lots of options, however getting it up and working wasn’t so simple as I had hoped. The method felt unnecessarily complicated and may gain advantage from a extra streamlined method.
Whereas the outdated GUI works, the interface feels outdated in comparison with trendy PCB design instruments. It’s purposeful, however the lack of intuitiveness and visible enchantment made it much less partaking for somebody like me who values simple navigation.
One other downside was the time it took for the dashboard to compute and course of evaluation. Even for easy designs, the wait felt unnecessarily lengthy, and I think about this concern might be extra pronounced with bigger, extra complicated initiatives. I anticipated the dashboard to ship fast insights, however the delays slowed down my workflow.
I additionally encountered some challenges with the constraint supervisor template creation and reuse. Whereas the constraint system is versatile, creating and reusing templates felt cumbersome. A extra intuitive method right here would considerably enhance the consumer expertise.
Lastly, I seen that help for importing legacy designs might be extra strong. Though I didn’t extensively take a look at this, importing older designs appeared like a time-consuming course of, and I might see this being a ache level for customers transitioning from different instruments.
What I like about PADS Skilled:
- The power to deal with complicated PCB layouts was a game-changer for me, particularly when engaged on intricate designs requiring exact management. This makes the instrument extremely efficient for detailed initiatives.
- The seamless integration with HyperLynx for Sign and Energy Integrity simulations gave me entry to superior evaluation capabilities, enhancing designs with highly effective insights.
What G2 customers like about PADS Skilled:
“It’s extremely useful for backend design and extremely dependable with glorious accuracy. The consumer interface is supportive {and professional}, making it simple to make use of repeatedly for designing and analyzing PCB fabrication. Integration is straightforward, and the shopper help from Mentor Graphics is excellent. General, it is simple to implement.”
– PADS Skilled Evaluation, Subhadeep P.
What I dislike about PADS Skilled:
- The outdated GUI felt much less partaking and lacked intuitiveness, making it tougher for me to navigate and totally benefit from the consumer expertise in comparison with trendy PCB design instruments.
- Because of its complexity, establishing the instrument initially was overwhelming, and a extra streamlined method would have saved me time and decreased frustration in the course of the onboarding course of.
What G2 customers dislike about PADS Skilled:
“One draw back of utilizing PADS Skilled is that it takes a major period of time to course of and compute analyses, even for one thing so simple as the dashboard, which could be fairly irritating.”
– PADS Skilled Evaluation, Souvik G.
4. Allegro X PCB Designer
I just lately explored Allegro X PCB Designer, and I discovered it distinctive for creating CPU motherboards and dealing with high-density interconnect (HDI) PCB designs.
Its capacity to develop compact, space-efficient electronics whereas sustaining superior performance is spectacular. The instrument makes it potential to pack intricate parts into smaller areas, a function that basically stood out to me and felt like a major benefit for contemporary electronics design.
Considered one of my favourite options was the error correction system for schematic design. With its three-step course of, it made guaranteeing schematic accuracy really feel intuitive and easy. It flagged errors early, corrected them logically, and validated the outcomes systematically, streamlining the design course of and minimizing potential errors.
I additionally appreciated the pre-analysis and post-analysis capabilities, which allowed me to catch and resolve points each earlier than and after the design part, making the complete workflow extra environment friendly and dependable.
The AI-based element automated the method of arranging parts on the PCB, saving me appreciable time. This automation additionally ensured exact and optimized placements that might sometimes require meticulous handbook changes. It felt just like the instrument was doing the heavy lifting, leaving me free to give attention to different points of the design.
I used to be additionally impressed by Allegro’s versatile workspace, which allowed me to customise the interface, instructions, and workflows to suit my private preferences. This adaptability was an enormous plus, because it made staying organized and productive a lot simpler. Aligning the instrument’s setup with my design habits felt like a good way to enhance effectivity and luxury.
Nonetheless, the lengthy load instances, particularly throughout resource-heavy operations, had been irritating. Whether or not it was beginning the appliance, creating library symbols, or working with parts, I seen important lag. This concern turned significantly noticeable when dealing with a number of 3D fashions or board mapping, which took for much longer than anticipated and felt like a bottleneck within the workflow.
One other limitation I noticed was the dearth of complete design for manufacturing (DFM) experiences. Whereas the instrument excels at creating PCBs, it doesn’t generate the detailed DFM experiences wanted to make sure a design is prepared for manufacturing. I had to make use of exterior instruments to fill this hole, which added an additional step and a few inconvenience.
Safety issues additionally stood out. The cadence.pcb information aren’t protected nicely and could be simply reverse-engineered. For these working with delicate designs, this lack of sturdy safety might pose important dangers.
Moreover, the absence of a direct VBScript interface means customers would possibly must be taught a brand new scripting language unique to Allegro. Whereas this may be useful for superior customization, the educational curve felt unnecessarily steep, particularly for many who aren’t accustomed to Allegro’s scripting surroundings.
What I like about Allegro X PCB Designer:
- Whereas testing Allegro X PCB Designer, I used to be impressed by its capacity to create compact and space-efficient designs for CPU motherboards and HDI PCBs. It confirmed actual potential for dealing with trendy, intricate layouts.
- The AI-based automation for arranging PCB parts stood out throughout my trial. It saved me time by optimizing placements and gave me a glimpse of how a lot effort it might eradicate in actual initiatives.
What G2 customers like about Allegro X PCB Designer:
“This software program is user-friendly and makes each pre-analysis and post-analysis simple to carry out. It contains built-in circuit (IC) enter/output buffer info Specification (IBIS) fashions for sign integrity and energy integrity evaluation. The software program provides varied forms of evaluation, equivalent to electrical evaluation, thermal evaluation, and eye diagram evaluation. It additionally synchronizes simply with seize and supplies floor-planning options. Moreover, auto-placement and auto-routing can be found, making the design course of extra environment friendly.”
– Allegro X PCB Designer Evaluation, Nikhil Ok.
What I dislike about Allegro X PCB Designer:
- Throughout my testing, I seen important delays when performing resource-heavy duties like dealing with 3D fashions or board mapping. These lengthy load instances made the workflow really feel much less environment friendly.
- I discovered the absence of complete DFM experiences limiting. To totally assess my take a look at designs for manufacturing readiness, I needed to discover exterior instruments, which added pointless complexity.
What G2 customers dislike about Allegro X PCB Designer:
“The software program must be backward appropriate with older revisions. It requires switching between totally different toolsets, and the complete workflow is not simply built-in. STEP export information do not work nicely with SolidWorks, and managing libraries and variants could be tough.”
– Allegro X PCB Designer Evaluation, Vijay P.
5. Autodesk Fusion
Throughout my testing of Autodesk Fusion, I explored a wide range of options, and it is clear that the software program has rather a lot to supply manufacturing groups.
One side that stood out to me was the 3D design and modeling instruments. These instruments are extremely highly effective and permit for the creation of each easy elements and sophisticated buildings.
A function I discovered significantly useful is manufacturing integration. Fusion permits designs to be taken straight by to manufacturing, which simplifies the method. As an alternative of switching between a number of platforms for design and manufacturing, every thing is consolidated in a single place. For manufacturing groups, this function is invaluable because it reduces the probabilities of errors and ensures all elements of the method are streamlined.
Fusion’s simulation and evaluation instruments permit for simulations like stress exams and movement evaluation, serving to manufacturing groups take a look at designs digitally earlier than transferring to manufacturing. By figuring out potential points, these instruments saved me time, at the same time as a newbie.
One of the vital modern options I examined was generative design. This instrument permits me to enter design objectives and constraints, and Fusion then generates a number of design choices that meet these standards. For manufacturing groups, this may be extremely helpful for exploring new design prospects and optimizing effectivity, because the software program suggests design options which may not have been thought of in any other case.
Nonetheless, I did encounter just a few challenges throughout testing. Assemblies in Fusion could be tough to handle, particularly when coping with bigger designs. Organizing and navigating by the totally different elements can turn out to be cumbersome, and it may be exhausting to shortly find particular parts when changes are wanted.
One other space the place I encountered some issue was with 2D drawings. Whereas Fusion does supply primary instruments for creating 2D drawings from 3D fashions, I discovered that the choices out there for detailed 2D designs had been restricted. For extra intricate drawings, I needed to export the design to AutoCAD to reap the benefits of extra superior instruments. This lack of flexibility within the 2D instruments might be improved for manufacturing groups that want detailed and sophisticated 2D representations.
Lastly, I bumped into some points with file conversion when exporting designs. Regardless of Fusion supporting many file codecs, I seen that some intricate particulars and geometries had been misplaced when the designs had been imported into different software program. This might be an issue for manufacturing groups that want exact, detailed designs preserved throughout totally different instruments.
What I like about Autodesk Fusion:
- Throughout my testing, the 3D design and modeling instruments in Fusion had been spectacular. I might simply create easy elements and sophisticated buildings, showcasing the software program’s energy for a spread of design wants.
- Fusion’s manufacturing integration function was an enormous benefit. I appreciated that I might take designs straight by to manufacturing without having to modify between platforms, making the complete course of extra streamlined and fewer error-prone.
What G2 customers about Autodesk Fusion:
“I like utilizing Fusion as an excellent 3D CAD program for creating elements or easy meeting designs. The format and capabilities really feel principally acquainted, and the small variations from different CAD software program I’ve used had been simple to regulate to. Fusion additionally appears designed with collaboration in thoughts, making it simpler to work collectively on designs (though I have never used this function a lot, I can see its worth). Considered one of Fusion’s largest benefits is its worth. I had hassle convincing administration to pay for 3D CAD software program because of the excessive prices, however Fusion was a lot simpler to justify, costing round 10% of what Inventor or SolidWorks would.”
– Autodesk Fusion Evaluation, Justin B.
What I dislike about Autodesk Fusion:
- Throughout my testing, I discovered it difficult to handle assemblies, particularly with bigger designs. Organizing and navigating by elements turned cumbersome, and finding particular parts shortly was tough.
- I encountered limitations with 2D drawings, the place Fusion’s primary instruments weren’t sufficient for creating detailed 2D representations. I needed to export designs to AutoCAD for extra superior choices, which added an additional step to the method.
What G2 customers dislike about Autodesk Fusion:
“Two points of Autodesk Fusion 360 that I discover much less favorable are its reliance on an web connection and its CAD file compatibility. Whereas being cloud-based provides important advantages, options like real-time collaboration and automated saving could be difficult in areas with restricted connectivity. Moreover, though Fusion 360 helps many file codecs, the conversion course of throughout export is commonly restricted, resulting in the lack of particulars or geometries when importing information into different software program.”
– Autodesk Fusion Evaluation, Juan M.
Unlock your design potential with highly effective prototyping software program. Begin constructing and testing your prototypes as we speak to deliver your concepts to life!
6. Altium CircuitMaker
After testing Altium CircuitMaker, I can confidently say that this instrument has rather a lot to supply, significantly for these engaged on circuit design. I discovered a number of options that basically stood out, though I additionally encountered just a few challenges alongside the way in which.
One of many options I appreciated essentially the most was the cloud integration. This allowed me to retailer all designs securely within the cloud, making them accessible from wherever. It was extremely handy, as I did not have to fret about dropping my work or managing cupboard space on my native machine. Moreover, the power to collaborate simply with others is a big plus. Whether or not you are working remotely or on a team-based mission, this cloud function makes it seamless to share and work on designs collectively. The cloud-based nature additionally means I did not should manually again up my information, which saved a major period of time.
One other function that basically made a distinction was the Fusion 360 plugin. This plugin allowed me to effortlessly bridge the hole between digital and mechanical designs. I might work on my circuit design in CircuitMaker after which seamlessly transfer to Fusion 360 to tweak the mechanical parts or vice versa. This fluid integration between the 2 platforms saved me hours of transforming and resolving alignment points, guaranteeing that my digital and mechanical designs aligned completely.
The 3D know-how for visualizing schematics was additionally a game-changer. Seeing designs in 3D helped me perceive how the circuits would work together as soon as they had been bodily constructed. It offered me with a a lot clearer image than conventional 2D views, and I used to be capable of spot potential errors early on which may have been missed in a 2D surroundings.
I additionally actually appreciated the power to simply assign properties to parts. Including feedback or particular attributes to elements helped me keep organized and maintain observe of modifications all through the design course of. It was significantly helpful for leaving reminders to myself or others about sure design selections or particular elements, guaranteeing nothing was missed.
The library that comes pre-loaded with Altium CircuitMaker is in depth and a real-time-saver. It contains a variety of symbols, footprints, and 3D fashions, so I didn’t should go looking for elements. I might entry not solely the elements themselves but additionally essential particulars like costing, stock info, and even distributor options. This made the designal course of a lot simpler, particularly once I didn’t have a pre-defined elements record. I might shortly pull up related parts and begin designing with out losing time on analysis or stock checks.
Nonetheless, there have been some challenges. Whereas the simulator mannequin works nicely for primary simulations, I discovered that the accuracy wasn’t at all times dependable for extra complicated circuits. The simulations typically didn’t precisely mirror real-world conduct, which made me query whether or not among the designs would operate as anticipated as soon as constructed. This might be problematic for extra intricate designs the place exact conduct is crucial.
One other concern I confronted was the lack to avoid wasting my initiatives offline. Because the mission file needed to be saved within the cloud, I couldn’t work with out an web connection. This was significantly inconvenient once I was in an space with poor connectivity or once I simply needed the flexibleness to work offline. Whereas the cloud integration is nice general, I’d have most popular the choice to avoid wasting initiatives regionally for added flexibility and safety.
Moreover, I discovered the heavy reliance on neighborhood sharing to be a little bit of a downside. Whereas the concept of sharing work with a big consumer base may be interesting to some, I personally choose extra management over my initiatives. The community-driven side felt a bit limiting, and I’d have favored extra independence in how my work is shared or stored non-public. For many who take pleasure in working independently, this might be a deal-breaker.
Lastly, as a Linux and MacOS consumer, I discovered the expertise lower than supreme. Since CircuitMaker is primarily designed for Home windows, I hadvert to arrange a digital machine to run the software program. Whereas it labored wonderful inside the digital machine, it added an additional layer of complexity to the setup. It wasn’t as seamless as utilizing a local utility, and I might see how this might be irritating for customers exterior of the Home windows ecosystem.
What I like about Altium CircuitMaker:
- I appreciated the cloud integration, which allowed me to retailer designs securely and entry them from wherever. It made collaboration simple, and I didn’t have to fret about backing up information manually.
- The Fusion 360 plugin was extremely helpful. It allowed me to seamlessly transition between digital and mechanical design, saving me lots of time by avoiding alignment points between the 2 platforms.
What G2 customers like about Altium CircuitMaker:
“CircuitMaker is a good instrument for designing and working electrical circuits. Its intuitive interface permits you to shortly draw, modify, and mix layouts with ease. It is a exact instrument that makes it easy to know the theoretical points {of electrical} circuits. With this system’s libraries, you possibly can create spectacular initiatives, and discovering a component is made simple by a nested construction inside subfamilies. This instrument contains all the mandatory options for use professionally in your organization or group.”
– Altium CircuitMaker Evaluation, James Michael W.
What I dislike about Altium CircuitMaker:
- I encountered points with simulation accuracy for complicated circuits. The simulator typically didn’t precisely mirror real-world conduct, which raised issues in regards to the reliability of designs for extra intricate initiatives.
- The lack to avoid wasting initiatives offline was a significant inconvenience. Because the information needed to be saved within the cloud, I couldn’t work with out an web connection, which restricted my flexibility in sure conditions.
What G2 customers dislike about Altium CircuitMaker:
“CircuitMaker enforces cloud saving and permits solely two non-public initiatives, which could be limiting. The neighborhood element library is unmoderated, containing many unusable footprints (although it is advisable to create your individual, because the element wizard makes it simple). The software program could be considerably unstable, so saving incessantly is essential. Moreover, the keyboard shortcuts differ from these in Altium Designer, which can take a while to regulate to.”
– Altium CircuitMaker Evaluation, Alberto V.
7. Autodesk EAGLE
One function of Autodesk EAGLE that stood out to me virtually instantly was the consumer language packages (ULP), the built-in programming language. It helped me save time by automating repetitive processes, which might be useful when engaged on a number of designs or making frequent changes. I might create customized scripts tailor-made to my wants, giving me larger management over the workflow. For manufacturing groups trying to velocity up manufacturing, this function could be a real-time-saver.
The autoroute operate is one other instrument that simplifies the design course of. In a producing context, the place time is crucial, the power to shortly route paths with minimal handbook effort was invaluable. It allowed me to generate fast prototypes and focus extra on refining the core design fairly than coping with routing points.
The instrument labored easily for schematic seize, which is essential in manufacturing for guaranteeing accuracy. It helped me spot potential points early, decreasing the probability of errors throughout manufacturing.
On the library administration facet, Autodesk EAGLE impressed me with its in depth number of pre-loaded CAD packages. This meant much less time spent looking for parts, permitting for sooner meeting and prototyping in manufacturing.
One draw back I encountered was with the 3D visualizer. Whereas purposeful, it didn’t supply the extent of accuracy I anticipated when visualizing how a PCB would look as soon as produced. In manufacturing, this degree of precision is crucial to make sure every thing suits collectively appropriately, and EAGLE’s 3D instrument didn’t fairly meet these expectations.
I additionally had points with the internet itemizing function, particularly when working with complicated energy PCBs. It didn’t at all times operate as anticipated, which led to delays and potential errors within the design part. Dependable internet listings are important for guaranteeing correct electrical connections within the last product.
One other limitation was the restriction within the downloaded model of EAGLE, which limits designs to simply two layers. This turns into a difficulty when working with extra complicated, multi-layer boards. For manufacturing groups engaged on high-density designs, this restriction could cause delays, forcing groups to discover different options or go for costlier variations of the software program.
Lastly, I really feel that routing intelligence might be improved. At the moment, EAGLE makes use of customary routing paths, however integrating AI-based routing algorithms would considerably enhance effectivity. This could lead to extra compact, optimized designs, velocity up manufacturing instances, and decrease routing-related errors.
What I like about Autodesk EAGLE:
- The consumer language packages (ULP) function stood out to me as a result of it allowed me to automate repetitive processes. Creating customized scripts saved me time and supplied larger management, particularly helpful for groups engaged on a number of designs.
- The autoroute operate was an actual time-saver for me. It shortly generated routing paths with minimal effort, enabling me to create prototypes sooner and focus extra on refining the core design as a substitute of coping with routing points.
What G2 customers like about Autodesk EAGLE:
“The CoA template was custom-made to satisfy our wants, together with all important consumer and pattern particulars, together with a desk displaying analytes and their noticed values. Every desk cell was designed to seize values based mostly on particular take a look at varieties. The CloudLIMS group collaborated carefully with us to make sure the template matched our expectations. They automated calculations and utilized built-in logic and sophisticated algorithms to make this occur.”
– Autodesk EAGLE Evaluation, Ronel C.
What I dislike about Autodesk EAGLE:
- I discovered the 3D visualizer to be a bit missing in accuracy. It didn’t present the extent of precision I wanted to visualise how the PCB would look as soon as produced, which might result in potential fitment points within the manufacturing part.
- I encountered points with the online itemizing function, significantly when working with complicated energy PCBs. It didn’t at all times work as anticipated, which prompted delays and will have led to errors in guaranteeing correct electrical connections for the ultimate product.
What G2 customers dislike about Autodesk EAGLE:
“The system’s session timeout is sort of restrictive, because the platform prompts session expiration after a brief interval. It will be useful if there have been an possibility to increase the session period, giving customers extra flexibility to finish duties with out the priority of dropping their progress.”
– Autodesk EAGLE Evaluation, Aryan Ok.
Greatest PCB design software program: incessantly requested questions (FAQs)
Q. How do I design a PCB?
To design a PCB, begin by making a schematic diagram that outlines the circuit parts and their connections. Then, use PCB design software program to transform the schematic right into a PCB format, putting parts and routing the traces. After finishing the format, generate the mandatory information for manufacturing, equivalent to Gerber information, and guarantee design guidelines and electrical constraints are met.
Q. Can I design a PCB on cellular?
Sure, some PCB design apps can be found for cellular units, although they have a tendency to have fewer options in comparison with desktop variations. These cellular apps are appropriate for primary design duties and easy initiatives, however for extra complicated designs that require superior performance, desktop software program is advisable as a result of its larger precision and complete toolsets
Q. How do I be taught PCB design?
You’ll be able to be taught PCB design by on-line programs, tutorials, and books that cowl electronics and circuit design. Start by understanding primary ideas like circuit schematics and element placement, after which apply utilizing free PCB design software program. Begin with easy circuits to construct your expertise earlier than progressing to extra complicated initiatives. Participating with on-line boards or communities can present helpful suggestions and steering, serving to you acquire confidence earlier than utilizing superior design instruments.
Q. How do I select the fitting PCB format design for my mission?
Choosing the proper PCB format design relies on elements just like the mission’s dimension, complexity, and required performance. Think about the variety of layers, the kind of parts used, thermal administration, and sign integrity. For prime-speed circuits, pay particular consideration to routing and grounding. Moreover, make sure the format meets any industry-specific necessities (e.g., automotive or medical requirements).
Q. Which is one of the best free PCB design software program?
Most high-quality PCB design software program instruments are paid, however many supply free trials that will help you get began. Altium Designer, for instance, is extensively considered among the best instruments within the {industry}, providing highly effective options for complicated designs. Its free trial could be a good start line. Discover extra free PCB design software program that provides primary options, which could be helpful for less complicated initiatives or newbies.
Preserve issues grounded
Choosing the proper PCB design software program could be a game-changer to your initiatives. When evaluating these instruments, it’s important to think about elements like usability, efficiency, and options that finest align along with your particular wants—whether or not that’s dealing with complicated designs, bettering sign integrity, or guaranteeing clean collaboration.
Based mostly on my testing and consumer suggestions, I’ve outlined the highest instruments that provide one of the best mixture of effectivity, flexibility, and energy. One of the best instrument is the one which works for you and helps you deliver your PCB designs to life with none hiccups.
Don’t be afraid to dive in, experiment with totally different choices, and see what clicks. Bear in mind, even essentially the most refined software program can’t assist when you don’t press the fitting buttons (until you’ve acquired a “design wizard” in your group, through which case, please share their contact information with me).
Scale back errors by utilizing simulation and take a look at suites earlier than transferring your PCB design to manufacturing.